鈦酸鉀晶須增強(qiáng)鋁基復(fù)合材料的研究現(xiàn)狀
時(shí)間:2005-07-05
摘 要:
對鈦酸鉀晶須增強(qiáng)鋁基復(fù)合材料的研究現(xiàn)狀進(jìn)行了綜述,主要介紹了鈦酸鉀晶須的特性,鋁基復(fù)合材料的制備工藝、界面結(jié)構(gòu)和性能,同時(shí)指出了目前存在的問題和進(jìn)一步研究的方向。
1 前 言
晶須增強(qiáng)鋁基復(fù)合材料由于具有高的比強(qiáng)度、比模量,良好的熱穩(wěn)定性,以及抗疲勞、耐磨損等性能而得到迅速發(fā)展,成為金屬基復(fù)合材料的一個(gè)重要分支。SiC和Si3N4晶須被認(rèn)為是鋁基復(fù)合材料最好的增強(qiáng)體,但價(jià)格昂貴[1]。國外特別是日本已開發(fā)出廉價(jià)的鈦酸鉀晶須,價(jià)格僅為SiC或Si3N4晶須的1/10~1/20,且復(fù)合材料有良好的切削加工性[2]。用其增強(qiáng)的鋁合金已用于軸承滑動(dòng)部件、活塞泵、發(fā)動(dòng)機(jī)汽缸套的隔熱內(nèi)襯等。
通常用K2O.nTiO2表示鈦酸鉀晶須的組成,n=1,2,4,6,8,它們在結(jié)構(gòu)和性能上差異顯著。其中以n=4,6即聚四和聚六鈦酸鉀的實(shí)用價(jià)值最大。聚六鈦酸鉀屬單斜晶系(空間群C2/m),晶格常數(shù)a=1.559 nm,b=0.382 nm,c=0.9112 nm,β=97.764°[3],其特性見表1:
表1 鈦酸鉀晶須的特性
化學(xué)式 |
K2O.6TiO2 |
熱膨脹系數(shù) |
6.8×10-6/℃ |
外觀形貌 |
白色針狀結(jié)晶 |
pH值 |
7~9(水中分散) |
晶須尺寸 |
直徑0.5~1.0 μm 長度10~40 μm |
熱導(dǎo)率 |
5.34 W/(m.℃)(25℃) 1.74 W/(m.℃)(760℃) |
耐熱溫度 |
1 200 ℃(在空氣中) |
比熱容 |
0.92 kJ/(kg.℃) |
真密度 |
3.3 g/cm3 |
電阻率 |
3.3×1013m.Ω(25℃) |
松密度 |
0.3 g/cm3 |
莫氏硬度 |
4 |
抗拉強(qiáng)度 |
7 GPa |
耐堿性 |
30%堿中,沸點(diǎn)下穩(wěn)定 |
彈性模量 |
280 GPa |
耐酸性 |
10%酸中,室溫下穩(wěn)定 |
2 復(fù)合材料的制備工藝
2.1 擠壓鑄造法[4]
將晶須、粘結(jié)劑和水混和,攪拌均勻后在模具中制成預(yù)制件,干燥后在900 ℃左右燒結(jié);將預(yù)熱至800 ℃左右的預(yù)制件放入金屬模具,注入750 ℃左右的鋁液后加壓至50~100 MPa,保壓1 min左右脫模。擠壓鑄造法容易實(shí)現(xiàn)工業(yè)化生產(chǎn),是快速生產(chǎn)復(fù)雜形狀復(fù)合材料零件的最有效的方法。但是,擠壓過程中易造成預(yù)制件壓縮變形,使復(fù)合材料中晶須的體積分?jǐn)?shù)難以控制。不同文獻(xiàn)對晶須體積分?jǐn)?shù)的報(bào)道差異較大,約在15%~55%之間[5,6]。同時(shí),高溫下鈦酸鉀晶須會(huì)與鋁液發(fā)生界面反應(yīng),影響復(fù)合材料的性能。
2.2 粉末冶金法[2,7]
將晶須與鋁粉末充分混和,然后在模具中進(jìn)行壓實(shí),再將壓實(shí)坯進(jìn)行熱壓;或晶須與鋁粉直接進(jìn)行熱等靜壓。為提高材料性能,還可將材料進(jìn)行后續(xù)加工,如熱擠壓等。粉末冶金法能準(zhǔn)確地控制晶須的體積分?jǐn)?shù),減少晶須與基體之間的界面反應(yīng),但是粉末混和時(shí)間長,成本高。晶須在混粉時(shí)易抱團(tuán),不易和鋁粉混和均勻;軋制過程中造成晶須的破斷等因素對復(fù)合材料的性能有不良影響。
3復(fù)合材料的界面結(jié)構(gòu)與界面反應(yīng)
國內(nèi)外對鈦酸鉀晶須增強(qiáng)鋁基復(fù)合材料的界面反 應(yīng)進(jìn)行了廣泛研究,并提出了各自的理論觀點(diǎn)。土取功等用差熱分析法證明,鈦酸鉀晶須在610 ℃與鋁發(fā)生界面反應(yīng),生成α-Al2O3,在950℃生成α-Al2O3和Al3Ti[8]。但是,管沼克昭認(rèn)為,鈦酸鉀晶須與基體在600~800 ℃左右反應(yīng)生成γ-Al2O3和TiO;TiO在晶須表面內(nèi)部形成,γ-Al2O3薄層覆蓋在晶須外表面[9]。最近,Li.J.H等使用高分辨率透射電鏡(HRTEM)的研究成果表明,用擠壓鑄造法制備的K2O.6TiO2W/ZL109復(fù)合材料在界面上生成TiO,MgTi2O4和MgAl2O4;T6處理會(huì)加重界面反應(yīng),Mg元素在界面處偏聚,使復(fù)合材料的強(qiáng)度有所下降。而對于K2O.6TiO2W/純Al復(fù)合材料,界面反應(yīng)產(chǎn)物僅為TiO[3]。
沈保羅等研究了用擠壓鑄造法制備的K2O.8TiO2W/ZL109復(fù)合材料,發(fā)現(xiàn)晶須與基體之間存在著TiO非晶態(tài)過渡層,在制造過程中,晶須的表面與基體已經(jīng)發(fā)生界面反應(yīng)[10]。在熱暴露或熱循環(huán)條件下K2O.8TiO2W/ZL109復(fù)合材料在500 ℃熱暴露100 h以上或熱循環(huán)5次以上晶須與基體會(huì)發(fā)生嚴(yán)重的界面反應(yīng),并有Ti7Al5Si12新相生成。熱循環(huán)比熱暴露更明顯地促進(jìn)了界面反應(yīng)[11]??梢?,晶須與基體的界面反應(yīng)及其機(jī)理研究是這種材料的一個(gè)重點(diǎn)。
4 復(fù)合材料的性能
鈦酸鉀晶須增強(qiáng)鋁基復(fù)合材料的性能優(yōu)異之處在于它的抗拉強(qiáng)度與熱膨脹系數(shù),如圖1和圖2所示??梢钥闯?,復(fù)合材料的常溫和高溫抗拉強(qiáng)度均高于基體;其熱膨脹系數(shù)比基體低得多,說明這種材料有較好的尺寸穩(wěn)定性。同時(shí),復(fù)合材料的硬度和彈性模量也有明顯的提高[4]。晶須的加入改變了鋁合金的凝固過程,細(xì)化了晶粒組織,同時(shí)在材料內(nèi)部產(chǎn)生了眾多晶須與基體之間的界面。這些界面阻礙位錯(cuò)的運(yùn)動(dòng),使位錯(cuò)產(chǎn)生塞積,從而使材料的性能得到了提高[12]。然而,過高的晶須體積分?jǐn)?shù)(≥40%)反而會(huì)降低復(fù)合材料的力學(xué)性能。因此,如何將晶須的體積分?jǐn)?shù)控制在適當(dāng)?shù)姆秶蔀榭刂茝?fù)合材料性能的關(guān)鍵。
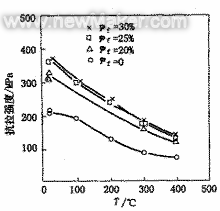
圖1 K2O.6TiO2W/Al復(fù)合材料的高溫抗拉強(qiáng)度
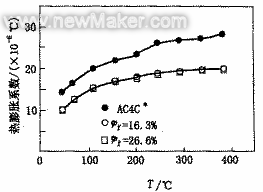
圖2 AC4C合金與K2O.6TiO2W/AC4C 復(fù)合材料的熱膨脹系數(shù)
復(fù)合材料的磨損性能與基體相比并無明顯的優(yōu)勢。在油潤滑條件下,K2O.8TiO2W/ZL109復(fù)合材料與基體相比,低載荷時(shí)兩者耐磨性差不多;高載荷時(shí)復(fù)合材料比基體更耐磨。一般認(rèn)為,低載荷下該復(fù)合材料的磨損機(jī)理是氧化-犁切-壓實(shí),氧化膜達(dá)到臨界厚度就發(fā)生脆性破壞。由于大量晶須的存在,使氧化膜變得并不完整,復(fù)合材料并不比基體耐磨。高載荷下是嚴(yán)重的金屬磨損控制磨損過程,復(fù)合材料中由于晶須的存在,塑性變形抗力增大,故比基體更耐磨[13]。也有人認(rèn)為復(fù)合材料的耐磨性差是因?yàn)殁佀徕浘ы毜挠捕鹊停?4]。從已有報(bào)道看,這方面的研究還不夠系統(tǒng)深入,晶須增強(qiáng)體的性能優(yōu)勢尚未得到充分的發(fā)揮。
5 研究展望
(1) 預(yù)制件的制備工藝。使用表面活性劑、超聲波振動(dòng)等方法使晶須團(tuán)、塊分散開,從而使晶須分散均勻。采用合適的粘結(jié)劑提高預(yù)制件的強(qiáng)度,減輕擠壓鑄造過程中預(yù)制件的變形,使復(fù)合材料中晶須的體積分?jǐn)?shù)能得到有效控制。
(2) 復(fù)合工藝和熱處理工藝。找出最佳工藝參數(shù),盡可能地減輕晶須與基體合金的界面反應(yīng),提高復(fù)合材料的綜合性能。
(3) 混雜使用。將鈦酸鉀晶須與其他復(fù)合材料增強(qiáng)物混和使用,發(fā)揮各自的優(yōu)勢,揚(yáng)長避短。
(4) 失效機(jī)理,包括磨損、腐蝕、疲勞的研究。